Anreize für die Manipulation von Schutzeinrichtungen
Teil 2 der Artikel-Serie in Kooperation von VDMA Elektrische Automation und GIT SICHERHEIT behandelt das Thema „Manipulationsanreize und die Normenlage bei Betriebsarten“ – im Interview mit Tobias Keller, Business Development Manager bei Schmersal, und Marcel Wöhner, Chief Technical Officer bei Pilz.
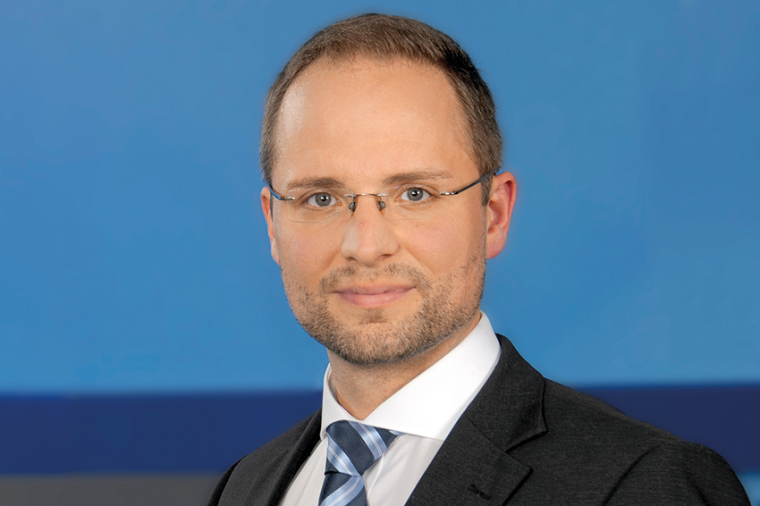
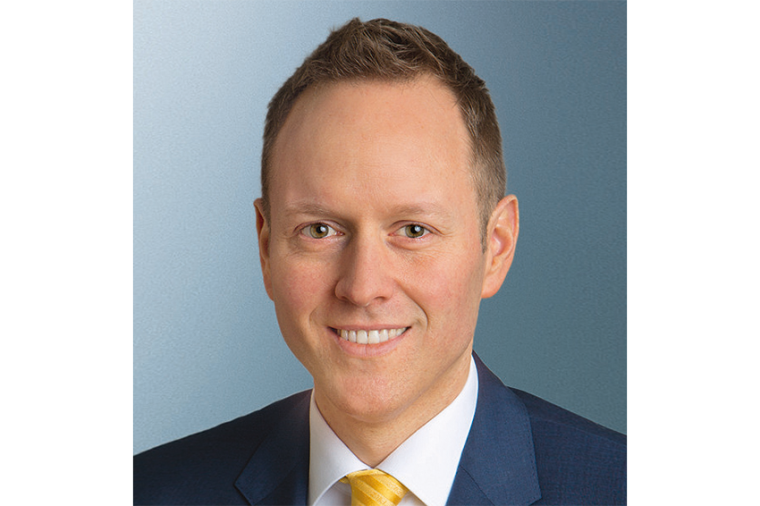
Manipulationsanreize und die Normenlage bei Betriebsarten
In Teil 1 der Artikel-Serie in Kooperation von VDMA Elektrische Automation und GIT SICHERHEIT standen die Ergebnisse der aktuellen IFA-Erhebung „Manipulation von Schutzeinrichtungen“ im Vordergrund. Diese machten deutlich, dass der Anteil ständig oder vorübergehend manipulierter Maschinen mit 27,2 % nach wie vor sehr hoch ist. Um so wichtiger ist es der Frage nachzugehen, welche Ursachen häufig und insbesondere Manipulationsanreize bedingen und wie sich die Normenlage bei den Betriebsarten gegenwärtig darstellt. Ließen sich über eine „passende“ Betriebsart für die Bedarfe bei der Instandhaltung die Anreize womöglich reduzieren? Um diesen Themen nachzugehen, stellen sich Tobias Keller, Business Development Manager – Solutions and Services bei K.A. Schmersal GmbH & Co. KG, und Marcel Wöhner, Chief Technical Officer – Subsidiary Germany bei der Pilz GmbH & Co. KG, den Fragen der GIT SICHERHEIT-Redaktion.
GIT SICHERHEIT: Herr Keller, fangen wir doch mit der naheliegendsten Frage an: Was sind die Anreize für Manipulationen an Maschinen und Anlagen? Welche Faktoren und Umstände üben den größten Einfluss auf die entsprechenden Verhaltensweisen aus?
Tobias Keller: Schutzeinrichtungen an Maschinen und Anlagen werden aus den verschiedensten Gründen manipuliert. Diese hängen im Wesentlichen von der Motivation bzw. der Zielsetzung der Person ab, die diese Manipulation vornimmt. Bspw. kann ein Beschäftigter Schutzeinrichtungen an Maschinen manipulieren, um die Produktivität und Arbeitsleistung zu erhöhen, indem er z. B. einen Sensor oder eine Sicherheitsabdeckung entfernt.
Ein weiterer wesentlicher Anreiz ist die Reduzierung von Ausfallzeiten und die Vermeidung von Produktionsverzögerungen. So kann die Schutzeinrichtung einer Maschine umgangen bzw. deaktiviert werden, sodass sie auch dann weiterläuft, wenn das Schutzkonzept in dieser Situation ursprünglich einen Stillstand vorsieht.
Manipulationsanreize sind immer dann gegeben, wenn sich der Mitarbeiter durch die Manipulation einen wesentlichen, auch persönlichen Vorteil durch das Umgehen einer Schutzeinrichtung verspricht. Dies kann ein erleichterter oder barrierefreier Arbeitsablauf oder auch nur eine Zeitersparnis sein. Es gibt immer einen Zusammenhang zwischen Ursache und Wirkung. Und die Ursache muss nicht immer unmittelbar an der Maschine zu finden sein!
In welchen Situationen kommt es denn am häufigsten zu Manipulationen – im Normalbetrieb oder doch eher bei Instandhaltungen?
Tobias Keller: Ich glaube, dass es gar nicht so sehr darauf ankommt, wann und in welcher Situation am häufigsten manipuliert wird. Wenn es um reine Zahlen geht, gibt es entsprechende Erhebungen. Vielmehr sollte die manipulierende Person mit ihrer Ausbildung und Erfahrung im Mittelpunkt der Betrachtung stehen. Ein Mitarbeiter, der in die Funktionsweise und Bedienung einer Maschine eingewiesen wurde, kann diese problemlos bedienen. Mit zunehmender Zeit an der Maschine wird er sich dann auch Gedanken über die „Optimierung“ seiner Arbeitsabläufe machen. Tatsächlich ist dies im Normalbetrieb einer der häufigsten Gründe für Manipulationen an Maschinen. Im Umkehrschluss kann hier bereits gesagt werden, dass ein durchdachtes und schlüssiges Sicherheitskonzept für den Normalbetrieb die Manipulationsanreize deutlich reduzieren kann. Eine nicht zu unterschätzende Unterstützung bieten hier die einschlägigen Normen und deren korrekte Anwendung.
Interessanter wird es jedoch mit zunehmender Fachkompetenz und Erfahrung der Mitarbeiter. Je tiefer das Verständnis für die Technologie und den Bearbeitungs- bzw. Produktionsprozess an der Maschine oder Anlage ist, umso weitreichender sind auch die Möglichkeiten der Manipulation. In diesem Zusammenhang muss dem Einrichter oder Instandhalter besondere Aufmerksamkeit geschenkt werden. Gerade in diesen Betriebsarten kommt es häufig vor, dass Sicherheitseinrichtungen „anders“ funktionieren als im Normalbetrieb. So lassen sich beispielsweise Linearachsen mit reduzierter Geschwindigkeit verfahren, obwohl die Schutzeinrichtung geöffnet ist. Dies ist seitens des Herstellers auch so vorgesehen, stellt aber dennoch ein erhöhtes Risiko für den jeweiligen Mitarbeiter dar.
Darüber hinaus kommt es sehr häufig vor, dass Manipulationen in Sonderbetriebsarten gar nicht als solche wahrgenommen werden. Mitarbeitern, die in diesen Betriebsarten an einer Maschine arbeiten, wird einfach per se unterstellt, dass sie dies in voller Kenntnis der damit verbundenen Gefahren tun. Nach dem Motto: „Die wissen schon, was sie tun!“
Nun gibt es aber auch Fälle, in denen sogar durch den Leitfaden der Maschinenrichtlinie (§239 – Wartung) ausdrücklich eingeräumt wird, „dass es sich nicht in allen Fällen vermeiden lässt, Gefahrenbereiche zu Wartungszwecken zu betreten, und dass bestimmte Einricht- oder Einstellarbeiten möglicherweise bei laufender Maschine durchgeführt werden müssen“. Herr Wöhner, können Sie unseren Lesern ein Beispiel für einen solchen Fall nennen?
Marcel Wöhner: Zunächst gibt die Maschinenrichtlinie zum Thema „Wartung der Maschine“ vor, dass alle Wartungsstellen außerhalb der Gefahrenbereiche liegen müssen oder die Maschine für die Wartung stillgesetzt werden muss. Sollte dies aus technischen Gründen nicht erfüllt werden können, dann müssen erforderliche Maßnahmen ergriffen werden. Hier gibt die Maschinenrichtlinie keine beispielhaften Maßnahmen als Orientierung für die praxistaugliche Auslegung der Maschine an die Hand. So kann es zum Beispiel gerade bei Instandsetzungsarbeiten vorkommen, dass gefahrbringende Bewegungen ausgelöst werden müssen. Zwar wäre das zum Beispiel bei geöffneter Schutztür mit zusätzlichem Zustimmtaster möglich, allerdings nur unter Einhaltung einer sicher reduzierten Geschwindigkeit für die bewegte Achse. Doch was, wenn sich dies beispielsweise mit Hydraulikzylindern oder pneumatischen Antrieben technisch nicht umsetzen lässt? Um den normativen Anforderungen genüge zu tragen, wäre dann die Ausführung der Bewegung nur hinter geschlossener Schutz-umhausung möglich.
Versetzen wir uns in den daraus resultierenden Arbeitsablauf: Zunächst würde der Instandsetzer den Gefahrenbereich verlassen und die Schutztüren schließen, um Bewegungen ausführen zu können. Dabei ist zu bedenken, dass hierzu gewisse Routinen notwendig wären und auch mehrere Schutztüren in weitläufigen Anlagen einbezogen werden müssten. Nach dem Ausführen der Bewegung würde die Schutztür wieder entriegelt werden, der Gefahrenbereich betreten und die Ergebnisse der Bewegung begutachtet. Im besten Fall könnten die Instandsetzungsarbeiten wieder aufgenommen werden. Allerdings müssten der komplette Ablauf aufgrund der fehlenden Einsichten in den relevanten Bereich sicher häufig wiederholt werden.
Und wie sieht es in einem solchen Fall dann mit den Anforderungen durch Richtlinien und Verordnungen aus – also wer haftet, falls dann doch etwas passiert?
Marcel Wöhner: Im geschilderten Beispiel wären die normativen Anforderungen erfüllt, jedoch könnte die Aufgabe kaum umständlicher gestaltet sein. Wie könnte hier eine Erleichterung für die Arbeitsaufgabe umgesetzt werden? Wird auf Betreiberseite manipuliert, so liegt die Haftung ebenfalls beim Betreiber. Beispielsweise könnte sich der Instandsetzer im Gefahrenraum einschließen lassen oder der Steuerung könnte „vorgetäuscht“ werden, dass die Schutzeinrichtungen geschlossen sind. Auch nachträgliches Abbauen von Schutzeinrichtungen findet häufig statt, wenn diese massiv als Behinderung der Arbeitsaufgaben empfunden werden. Würde der Maschinenhersteller den Forderungen des Betreibers nachkommen, dass Antriebe für gewisse Tätigkeiten auch bei geöffneten Schutztüren betrieben werden sollten, handelt er vorsätzlich gegen normative Vorgaben.
Sie sehen also, dass wir in einer schwierigen Zwickmühle sind. Denn auch wenn der Hersteller einer Maschine die Notwendigkeit einer solchen Betriebsart erkennt, gibt es für die Umsetzung (bisher noch) keine Orientierungshilfe wie beispielsweise technische Regeln. Die normativ beschriebene sichere Betriebsart „Service“ wird hierfür meist implementiert. Jedoch bleibt diese Betriebsart in der Regel nur für die eigenen Servicemitarbeiter des Herstellers vorbehalten. Das liegt daran, dass es hierfür eine hohe Auflage an organisatorischen Maßnahmen wie spezieller Schulungen und Unterweisungen bedarf.
Der bereits genannte Leitfaden der Maschinenrichtlinie fordert ja in diesem Zusammenhang eine „geeignete sichere Betriebsart“: Wie sollte diese konkret gestaltet sein? Und welchen Einfluss hätte das auf die Fragen nach der „Haftung“?
Marcel Wöhner: Eine sichere Betriebsart müsste man unter verschiedenen Gesichtspunkten betrachten. Zunächst ist die Analyse der eigentlichen Aufgabe das Wichtigste – also dass man sich genau die Wartungs- und Instandsetzungsaufgaben anschaut und festlegt, welche Bewegungen und Funktionen an der Maschine dafür notwendig sind. Diese Arbeiten dürfen den Instandsetzer nicht in Gefahr bringen. Also muss überlegt werden, wo sich die Person bei den Arbeiten aufhalten darf und wie sie vor den Gefahren geschützt wird. Wenn Arbeiten im Gefahrenbereich ausgeführt werden, dann muss sichergestellt sein, dass Achsbewegungen erstens nicht unabsichtlich erfolgen und zweitens nicht von jedem ausgeführt werden können. So muss auch die Anwahl dieser speziellen Betriebsart über eine sichere Einrichtung erfolgen und auf definierte Personengruppen einzuschränken sein. Sprich, der Schlüssel für die Betriebsart darf nicht permanent am Pult stecken und die Umschaltung muss durch die Sicherheitssteuerung erfolgen.
Hier kommen zu den technischen auch organisatorische Maßnahmen hinzu, um das Personal zu schützen. Der Hersteller wird diese Maßnahmen beschreiben und ermöglichen. Der Betreiber ist dazu verpflichtet, sie umzusetzen und einzuhalten.
Im Fall der Haftung würde ein Staatsanwalt vermutlich weniger nach der Praxis-tauglichkeit der Maßnahmen entscheiden. Wurde manipuliert, dann muss sich der Betreiber verantworten. Wenn nicht manipuliert wurde, ist die Frage: Hat der Hersteller die Vorgaben der gültigen C-Normen eingehalten? Wo Hersteller technisch begründet abweichen, wird man sie in der Haftung sehen. Eine enorme Entlastung für Hersteller und Betreiber wäre eine technische Regel oder normative Ergänzung, damit sich die Beweislast vor Gericht umkehrt. Auch würden sich damit einheitlichere Lösungen als Stand der Technik durchsetzen. Das würde das Unfallrisiko ebenfalls reduzieren.
Zum Abschluss wäre es interessant zu erfahren, welche Auswirkung eine solche Richtlinie im Idealfall auf die Anreizstrukturen für Manipulationen hat?
Tobias Keller: Im Idealfall würde sich eine solche Richtlinie durchaus positiv auf die Minimierung der Anreizstrukturen zur Manipulation von Maschinen und Anlagen auswirken. Meines Erachtens sollte jedoch bei derartigen Richtlinien in Zukunft noch mehr Wert auf die Erhöhung des Gefahrenbewusstseins als auf die reine Formulierung technischer Anforderungen gelegt werden. Die Anwender der Richtlinien sollten im Idealfall ein Bewusstsein dafür entwickeln, womit sie es zu tun haben und vor allem warum sie es tun. Gefahrenbewusstsein und Methodenkompetenz in einer Richtlinie vereint, wäre ein großer Schritt in die richtige Richtung. Diesen Schritt sehe ich auch.
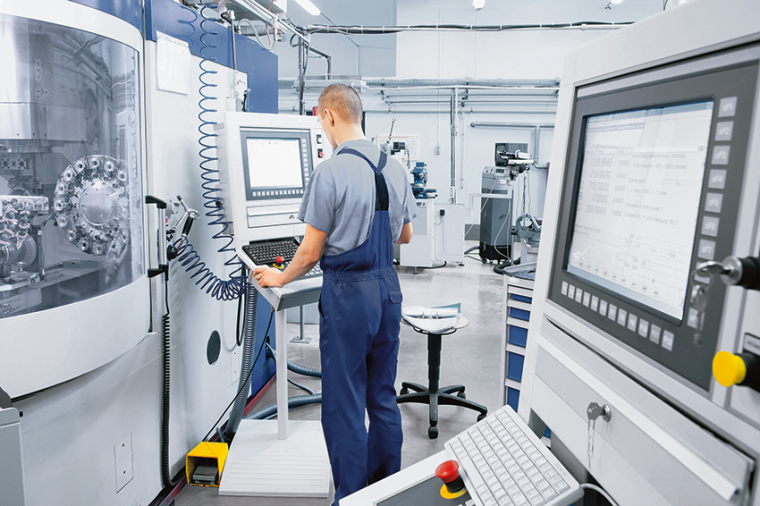
Business Partner
VDMA Verband Deutscher Maschinen- und Anlagenbau e.V.Lyoner Str. 18
60528 Frankfurt
Deutschland
Meist gelesen
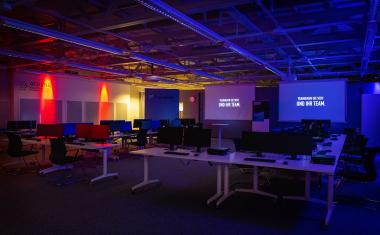
Risikovorsorge durch Cybertrainings – realitätsnah auf der "Cyber Range"
Wird ein Unternehmen Opfer eines Cyberangriffs, dann haben sich Angreifer in der Regel über längere Zeit in mehreren Schritten zu ihrem Ziel vorgearbeitet
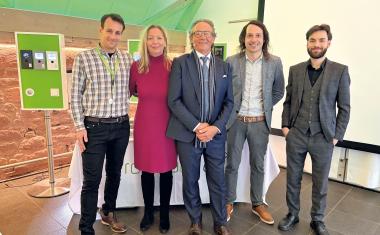
Frogblue International Partner Conference 2025: Innovationen und Zukunftsvisionen
Die Veranstaltung bot eine Plattform für den Austausch von Innovationen, Strategien und Zukunftsvisionen im Bereich der Gebäudeautomation und Zutrittskontrolle bis hin zu Einblicken in Kameratechnik.
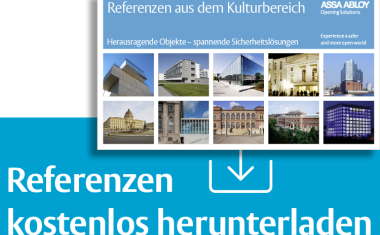
Zutritt steuern, Werte schützen – Schließtechnik für Kulturstätten
Öffentlich zugängliche Kulturinstitutionen sind mit unschätzbaren materiellen und immateriellen Werten ausgestattet.

VIP-Interview: Andreas Maack, Chief Security Officer bei Volkswagen
GIT SICHERHEIT im Interview mit Andreas Maack, Leiter Konzern Sicherheit & Resilienz und Chief Security Officer der Volkswagen AG.
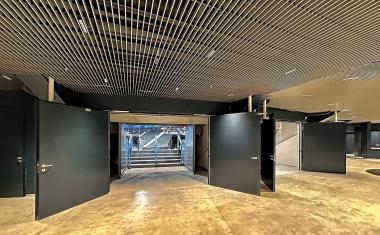
Brandschutztore für den SAP Garden in München
Diese multifunktionale Arena, die Platz für bis zu 11.500 Zuschauer bietet, eignet sich zudem für eine Vielzahl von Veranstaltungen und erfordert dementsprechend höchste Sicherheitsstandards.